
Breaking the Mold: Transforming Bihar’s Brick Kilns
As the winter chill settles in, thousands of brick kiln workers in Bihar are busy molding, stacking and firing countless rounds of clay. For these workers, the brick-firing season – typically October to June – is an essential livelihood opportunity. One of India’s largest brick manufacturing hubs, Bihar is home to approximately 7,865 brick units and produces over 23 billion bricks annually. But beneath its success lies a heavy dependence on coal and labor-intensive practices.
A transformation is underway, offering hope for a more sustainable future. At the heart of this shift is the adoption of zigzag kiln technology, a cleaner and more efficient alternative to the traditional Fixed Chimney Bull’s Trench Kiln (FCBTK). While promising, the transition is not without challenges.
The Case for Zigzag Kilns
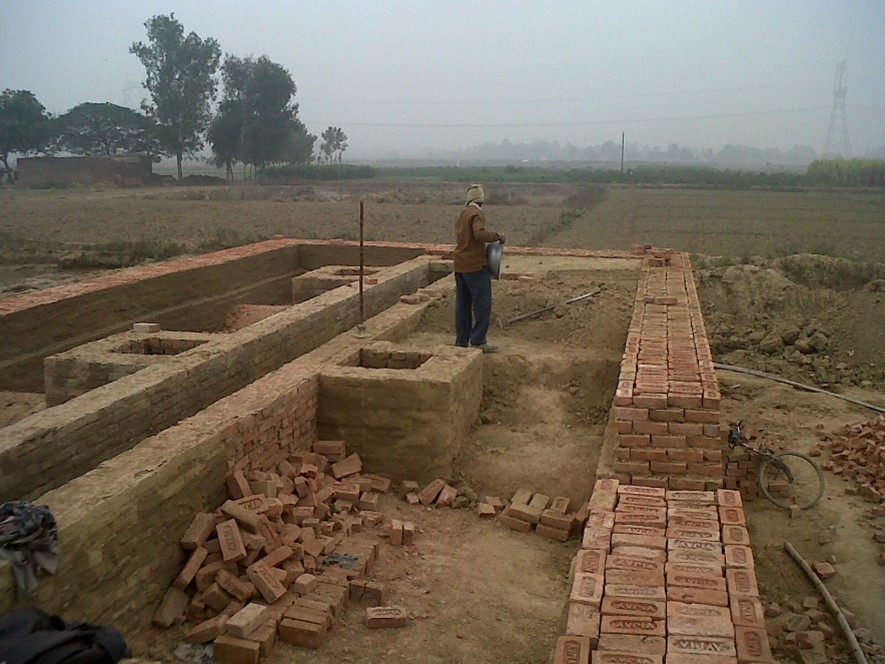
Following a December 2015 directive by the Central Pollution Control Board, several states have directed brick kilns in their jurisdiction to shift from FCBTK to zigzag kiln technology. Zigzag kilns use a natural draft mechanism to channel airflow in a zigzag pattern, ensuring uniform combustion. This method reduces coal consumption by 20%, cuts emissions of black carbon and particulate matter by 75%, and lowers energy use by 20%.
Besides offering environmental benefits, the improved process enhances brick quality and reduces breakages, improving production efficiency. A performance assessment study revealed that zigzag kilns produce about eight bricks per kilogram of coal compared to five bricks with FCBTKs. Retrofitting an FCBTK kiln to zigzag costs around ₹40 lakhs; however, the investment often pays off within one to two years through savings on fuel and improved output.
What are the Challenges?
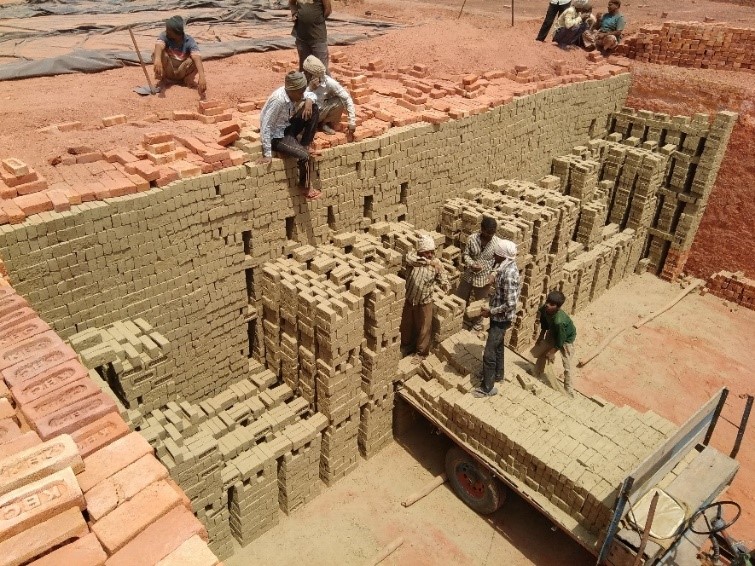
Transitioning to zigzag kilns demands not only technological upgrades but also a skilled workforce to ensure efficiency and quality. Each kiln employs 120–150 workers in roles such as molders (Patheras), stackers (Beldars), loaders (Kumhars) and firepersons (Jalaiwalas). Most workers learn on the job and lack the formal training needed for operating zigzag kilns. The technical precision needed for stacking and firing bricks directly affects productivity. A kiln owner from Jamui district acknowledges, “We have switched to zigzag, but without trained workers, achieving full efficiency is challenging.” A recent study revealed that 43% of kilns in Bihar struggle with inefficiencies due to untrained labor.
Harsh working conditions further compound these challenges, as many workers live in cramped, temporary housing for months, enduring exposure to coal dust, intense heat and long hours. Female workers, who represent only 13% of the workforce, face additional barriers, including cultural norms, safety concerns and limited access to skill development programs. The dual burden of physical labor and household responsibilities further exacerbates their struggles, underscoring the need for targeted training and worker welfare initiatives.
Training Initiatives and Capacity Building Exercises
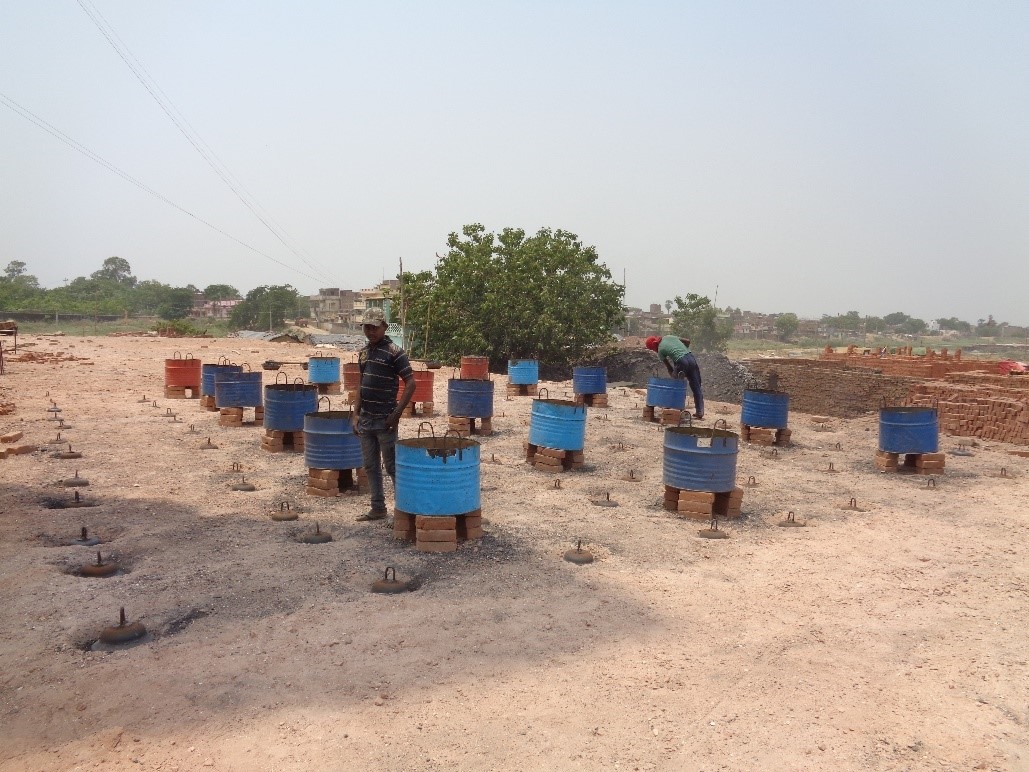
Operational challenges due to limited knowledge of firing processes, brick stacking techniques and retrofitting practices have led to kiln shutdowns in districts such as Champaran, underlining the need for targeted training and capacity building.
To address these needs, not-for-profit organizations have partnered with the state government and industry stakeholders to support capacity-building initiatives. For instance, Greentech Knowledge Solutions and Development Alternatives have developed training modules in Hindi, distributed by the Bihar State Pollution Control Board (BSPCB), to help masons and contractors understand zigzag kiln requirements. Since 2016, training programs have been offered to both workers and kiln owners, covering essential skills such as brick stacking, firing techniques and operational efficiency. “Training has been transformative,” says a kiln owner from Patna. “We’ve seen not just cost savings but also improved working conditions and brick quality.”
The Way Forward
Bihar must adopt an integrated approach that combines technological advancements with a strong focus on worker welfare. Central to this transition is the expansion of training programs. Partnerships between industry stakeholders, government agencies and non-profit organizations can help workers acquire these essential skills. Formal certification programs should also be introduced, enhancing workers' employability.
Equally important is strengthening policy implementation. While the BSPCB has mandated cleaner technologies, enforcement remains inconsistent. Real-time monitoring of unregulated kilns can drive faster adoption of sustainable practices.
Another key to long-term sustainability is the promotion of nearly zero-emission alternatives like fly ash bricks. While zigzag kilns represent a significant step forward, fly ash bricks could reduce emissions even further. Government incentives, such as subsidies and low-interest loans, can encourage kiln owners to make this transition.
Finally, improving worker welfare is critical. Providing workers with safety equipment, health screenings, access to clean drinking water and heat shelters can vastly improve their quality of life. Addressing systemic issues such as income stability and gender inclusivity will further ensure that the transition is equitable and sustainable.
Bihar’s brick kiln industry stands at a crossroads. The shift to cleaner technologies like zigzag kilns requires not just technological upgrades but also a commitment to worker skilling and welfare. With targeted investments, strong policy measures and capacity-building initiatives, Bihar can transform its brick kilns into a model for sustainable industry practices.
Faiza Solanki is former senior program associate and Isha Verma is former senior communications associate, Climate, Economics and Finance Program, WRI India.