
Emission Reduction Potential of Green Hydrogen in Ammonia Synthesis for Fertilizer Industry
The second blog of our three-blog series on the Indian fertilizer industry discusses the requirement of ammonia as an intermediate in the manufacturing process of fertilizers and the role of hydrogen as a feedstock in ammonia synthesis. Read the first and third blog of the series.
The fertilizer industry consumes hydrogen in the form of ammonia, primarily to produce urea, diammonium phosphate (DAP) and other complex fertilizers. Each ton of ammonia production requires roughly 178 kgs of hydrogen. To produce hydrogen, feedstocks such as natural gas, naphtha, or coal are employed. However, compared to others, natural gas is the most hydrogen-rich feedstock. The amount of ammonia required for manufacturing fertilizers is shown in the following table.
Fertilizer | Ammonia Requirement |
---|---|
Urea | 570 kg |
DAP | 200 kg |
Table 1: Ammonia requirement in the production of major fertilizers
In India, all urea plants have slowly transitioned to using natural gas as a feedstock due to good natural gas pipeline connectivity. A few plants avoid using natural gas and instead use coal for power and steam production because it reduces the cost of energy and hence lowers the cost of fertilizer production.
Pure hydrogen is not present in the reactor during ammonia synthesis. It is instead fed into the reactor as a mix with nitrogen, after the steam methane reforming (SMR) process. The reforming of hydrocarbons for hydrogen accounts for two-thirds of the total emissions in the ammonia synthesis plant while the remaining comes from the combustion for energy requirements. For instance, the stationary combustion of natural gas generates significant emissions in the form of carbon dioxide, methane, nitrous oxide and other greenhouse gases, resulting in total emission of 2.67 kg carbon dioxide (CO2) equivalent.
The total emissions are highest when ammonia is synthesized using hydrogen obtained from coal gasification. Therefore, it is critical to transition hydrogen production away from the coal gasification pathway to reduce emissions. The CO2 footprint and energy requirement for ammonia synthesis using other production pathways is shown in Figure 1, based on the best available technology.
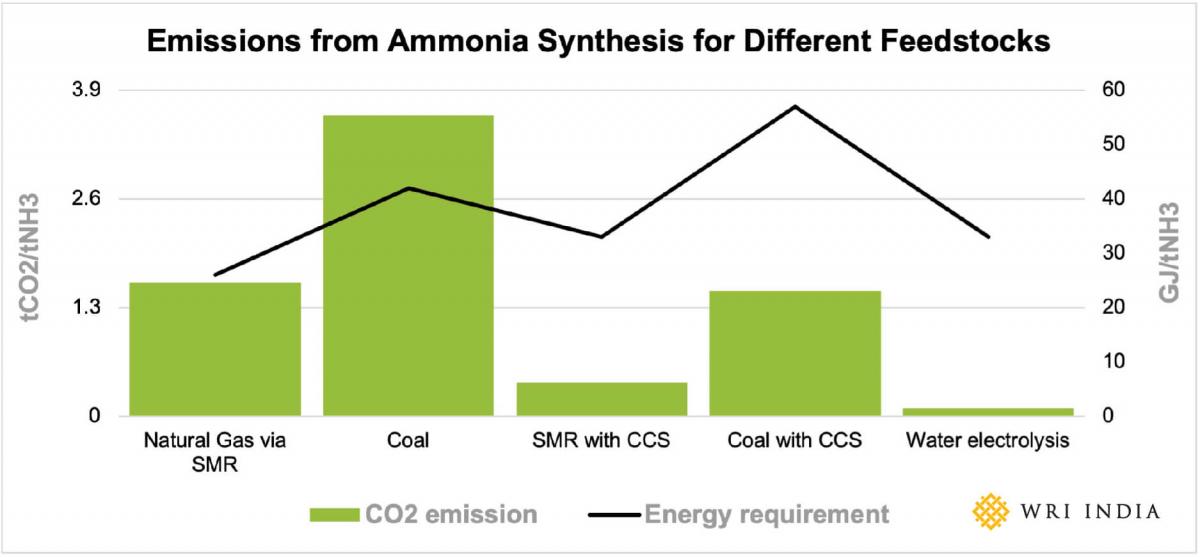
For 1kg of hydrogen production, 3.4 kgs of natural gas is required in SMR while 7.9 kgs of dry coal is required in coal gasification process. The CO2 emissions in ammonia synthesis depend on the feedstock used. The following table shows the emission in hydrogen production using different feedstocks.
Pathways | Global warming potential (kg CO2eq/ kg H2) |
---|---|
SMR | 12.13 |
Coal Gasification | 24.2 |
SMR with CCS | 3.4 |
Gasification with CCS | 4.08 |
Water electrolysis | 2.21 |
Table 2: Comparison of the emissions in hydrogen production using different feedstocks
Compared to all conventional processes, hydrogen production through water electrolysis has the lowest emissions. Using green hydrogen in the manufacturing process could help mitigate the emissions considerably. If 19.1081 MTPA (million tons per annum) ammonia production in India transitions to green hydrogen, emissions of up to 30.6 MTPA can be averted across the country.
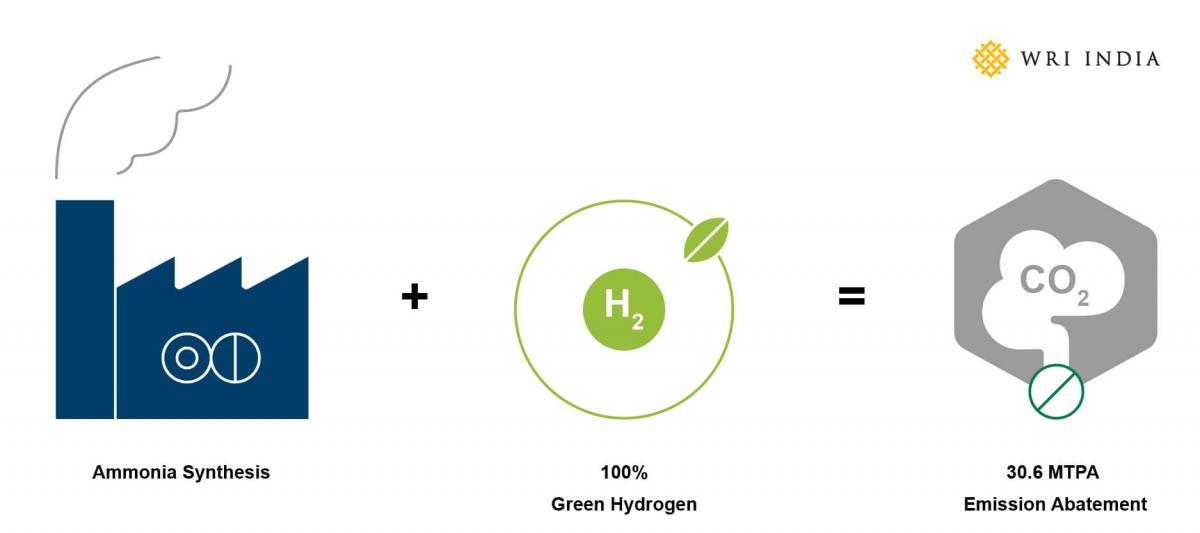
To reduce emissions, there is a need to efficiently integrate green hydrogen into the fertilizer manufacturing process. Technology providers including Hader Topsoe claim that with minor changes, existing ammonia manufacturing plants can consume up to a 10% blend of green hydrogen in their total hydrogen requirement using a hybrid arrangement. This hybrid setup can be an important enabler for green hydrogen in the ammonia plants to drive initial emission reduction. The conventional ammonia production process will provide the economies of scale and the blending of green hydrogen will bring down the overall emissions in a hybrid setup. While this arrangement cannot completely phase out grey hydrogen from the production process, it will help initiate the transition to green hydrogen to a point where the cost of infrastructural modification/addition is minimal.
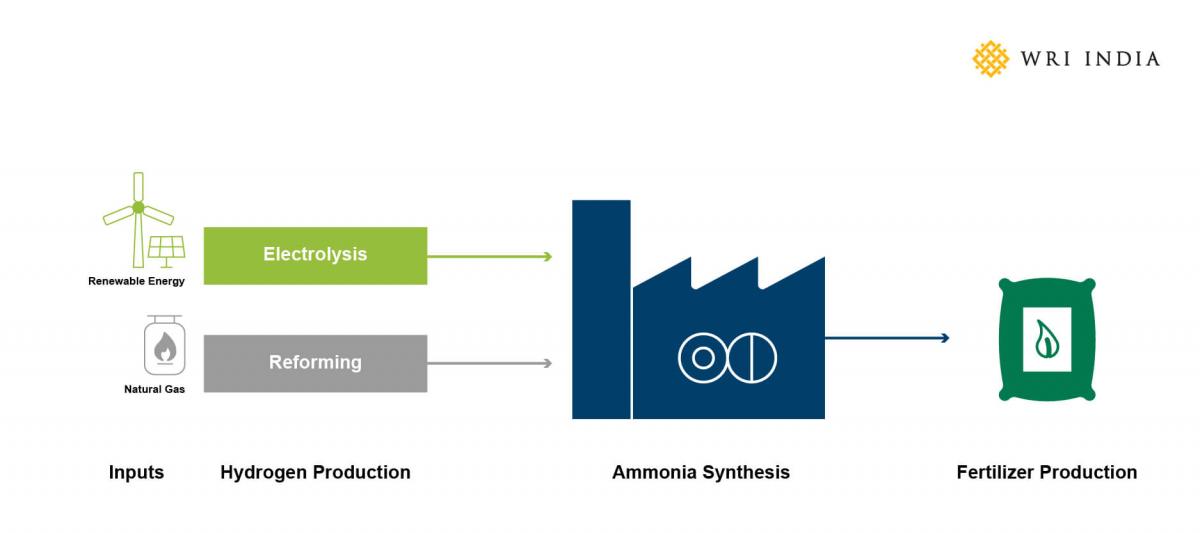
Considering global trade experience of over 75 years in handling ammonia, both its synthesis and storage involve efficient and mature technologies. Most fertilizer plants and ports have provisions for ammonia storage and as a hydrogen carrier, ammonia can be easily be integrated into hydrogen demand centres such as a hydrogen hub.
Incorporating green hydrogen in fertilizer manufacturing is crucial to eliminate emissions completely by modifying production infrastructure. There can be two approaches to achieving this. One could be to directly mix green hydrogen with synthesis gas prior to the synthesis loop at the fertilizer plant. Another could be to keep the manufacturing of green and grey ammonia independent and feed a mixture of the two for fertilizer production. Procuring green ammonia directly for manufacturing ammoniacal fertilizers can also be considered by manufacturers to avoid major modifications at integrated plants.
The barriers while incorporating green hydrogen in the manufacturing process for the fertilizer plants will be discussed in the last blog of this series.
Views are personal.